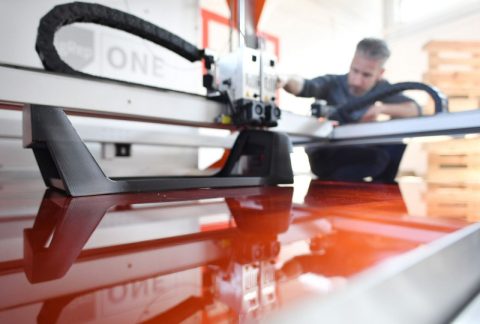
3D kan de tijd nodig voor onderhoud treinen helpen verkorten
Door de grote vooruitgang in de 3D-technologie is het mogelijk onderdelen snel te vervaardigen zonder ze te hoeven bestellen of in voorraad te hebben.
Om een maximale betrouwbaarheid in de dienstverlening via het spoor te garanderen, zijn tegenwoordig vaak minimale hoeveelheden aan reserveonderdelen vereist. Ze zijn ook vaak opgenomen in het ordercontract en in sommige grote depots nemen ze onnodig veel ruimte in beslag.
Dit resulteert in een voorraad aan reserveonderdelen en gereedschappen die niet altijd dagelijks nodig zijn. Wat uiteraard een prijs heeft, want ook opslag kost geld.
Vele jaren na hun ingebruikname zijn reserveonderdelen voor rollend materieel anderzijds vaak moeilijk te verkrijgen. Net als andere operators in Europa zet Deutsche Bahn in op 3D-printen voor het aanleveren in de toekomst van de reserveonderdelen voor zijn treinen. Zo kan stilstand van het rollend materieel worden verminderd.
3D biedt wel degelijk kansen
Daniela Gerdtom Markotten, directeur Digitalisering en Technologie bij DB, legt de uitdaging uit: “Onze treinen moeten rijden voor onze klanten en niet werkloos in de werkplaats staan. 3D-printen stelt ons in staat om sneller reserveonderdelen te vinden en onderdelen die niet langer beschikbaar zijn zelf opnieuw te bouwen”.
Snel en op maat gemaakt
Dankzij het 3D-printproces kan DB in korte tijd reserveonderdelen printen die anders lange levertijden zouden vragen of zelfs helemaal niet meer beschikbaar zijn.
In Neumünster, in Sleeswijk-Holstein (het noorden van Duitsland), heeft Deutsche Bahn ongeveer 350.000 euro in de 3D-technologie geïnvesteerd. Voor de groep als geheel gaat het tot nu toe om zo’n 750.000 euro. Volgens het management moeten tegen 2030 ongeveer 10.000 componenten kunnen worden vervaardigd door middel van 3D-printen, wat overeenkomt met ongeveer een tiende van de onderdelen die worden gebruikt bij het onderhoud van voertuigen.
Meer dan 100 verschillende onderdelen worden door DB vandaag al door middel van 3D-printen vervaardigt, waaronder waaierwielen, hoofdsteunen voor regionale treinen, de meest uiteenlopende behuizingen of zelfs kleine onderdelen met een belangrijk toepassinsgebied: reserveonderdelen voor koffiemachines en kapstokhaken voor ICE-treinen.
Veelbelovende resultaten
Alle 3D-geprinte componenten ondergaan uitgebreide tests voordat ze worden gebruikt, zoals tests op de weerstand tegen vermoeiing. Additive manufacturing, d.w.z. constructie in lagen, maakt het ook mogelijk om reserveonderdelen vooraf te optimaliseren op bijzonder storingsgevoelige punten.
Dit minimaliseert de kansen op slijtage en verhoogt de beschikbaarheid van de treinen. Terwijl de eerste bedrukte onderdelen uitsluitend van kunststof, meestal polyamide, werden gemaakt, worden nu ook metalen onderdelen geproduceerd met behulp van het poederdrukproces.
3D printen maakt het mogelijk om eventuele knelpunten in de levering te omzeilen en bespaart tevens kosten. Naast de eigen 3D-geprinte reserveonderdelen, werkt het spoorwegbedrijf ook samen met gespecialiseerde bedrijven en koopt het bijvoorbeeld 3D-geprinte metalen onderdelen in.
Sneller, minder arbeidsintensief en soms goedkoper
Het gebruik van deze techniek is ook sneller, minder arbeidsintensief en soms goedkoper dan kopen via conventionele middelen.
Sinds 2015 heeft Deutsche Bahn meer dan 30.000 3D-geprinte onderdelen gebruikt voor 500 verschillende toepassingen. Aanvankelijk licht en klein stelt 3D-printen DB nu in staat onderdelen te bouwen met een gewicht tot 27 kilo voor zijn ICE’s.